Understanding Metal Trimming Process Manufacturing Technologies
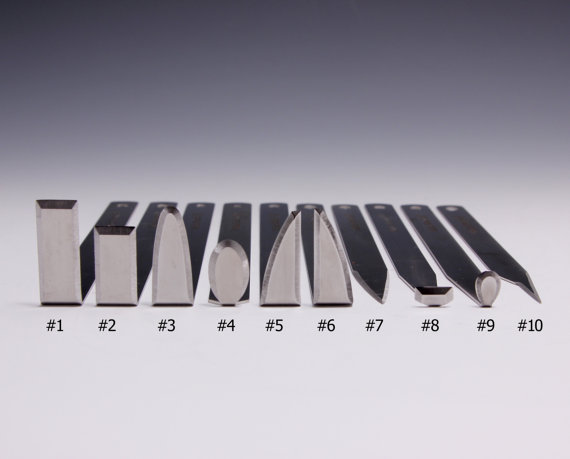
A common question in the metal trimming industry is: what metal trimming process manufacturing technology makes the most sense? Unfortunately, this is not a simple question that can be covered in a simple statement. There are many factors to this answer including the type of metal being cut, thickness, how the quality of the trim is defined, and the timeline for completion. With so many variables and metal trimming process manufacturing technologies, how does one make the right decision? First, you must understand the available options.
Types of Metal Trimming Process Manufacturing Technologies
There are four primary types of metal trimming available including:
Laser
Lasers emit a low-divergence beam of line with a defined wavelength that can trim metal. Most laser trimming machines are powered by a CO2 resonator that ranges in power from 1.5 kW to 6 kW. In the early days of this technology, lasers were limited to only trimming thin sheet metal. Since more powerful resonators have been developed, lasers are now capable of cutting steel up to 1.5 inches thick. It is important to consider when using this technology, the more reflective the part, the laser may have difficulty due to the bounce-back of the light.
Oxyfuel
The oxyfuel process utilizes a torch that heats the metal to kindling temperature. The focused oxygen stream reacts with the metal through a chemical process thus oxidizing the part and blowing it away to create the trim. Heat is a byproduct of this process, so it is typically used for cutting mild steel with a thickness range of 3/8-inch to 12-inches. There are high tolerances associated with oxyfuel B2B online marketplaces trimming.
Plasma
The plasma trimming process manufacturing technology involves heating gas to a high temperature where it ionizes. This produces an electrically-conductive, ionized gas known as plasma. A high-velocity jet of plasma is delivered to a metal piece with an electrical arc thus melting the metal. The stream of ionized gas then blows away the molten metal. Plasma cutting yields various quality and speeds, depending on the metal, desired quality, thickness, and required speed. In summary, the more power you produce, the faster the trimming process but plasma trimming is not as precise as other options.
Waterjet
Waterjet is the same as rapid erosion. Waterjet trimming utilizes a high-pressure water pump to force water through a nozzle where it is mixed with abrasive, like aluminum oxide or garnet. This combination rapidly erodes the metal where the nozzle is aimed. Within the metal trimming world, the technologies are incredibly competitive regarding cost per part. The waterjet process is ideal for shops that must cut various materials, not only metal. Waterjets can also cut rubber, glass, and various plastics.
The waterjet process is popular with metals because it produces a clean trim without creating heat thus eliminating distortion around the cut. A waterjet machine can slice through thin sheet metal up to 12-inches thick if required. Remember, the thicker the material is the wider tolerances that occur, and cutting cycle times increase.