Everything you need to know about PCD Cutting Tools
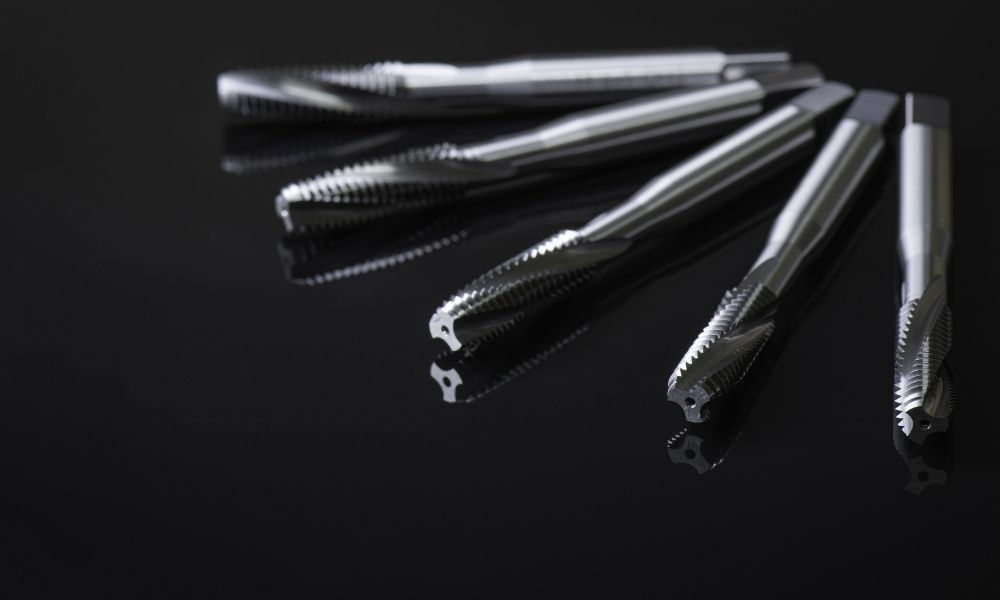
Diamond is the most complex material in nature with unique qualities, including abrasion resistance. This quality makes a diamond a desirable candidate for cutting tools in the manufacturing industry. With high durability and cutting speed, the Polycrystalline diamond tool’s usage in non-ferrous processing materials will improve its performance.
Polycrystalline Diamond
As specified earlier, PCD tools are highly resistant and have unsystematically oriented diamond crystals bonded to a sub-stratum of tungsten carbide. Synthetic diamonds are created under high temperatures and pressure in a laboratory. Cobalt alloy fills the empty spaces between PCD grains, making the final product sturdy. Continue reading to know the benefits of these diamond tools.
Long-lasting tools offer consistent results.
If you are using solid carbide tools, they last for only a few days or weeks. Highly intense production levels can reduce the tool life, which increases the demand for PCD tooling. These PCD products can be used for several months, assuring high-yield production and less downtime.
Top-notch performance
PCD tools perform faster than solid carbide tools so you can expect high efficiency and effectiveness. It will speed up the task and also decrease the lead time.
Some tasks like grinding and deburring can take time, costing you a lot. Polycrystalline diamond tools are the best tools that you can use for accurate operation without spending more time, money, and energy.
Versatile to use
Previously, polycrystalline diamond tools were used for only a small group of materials. However, the evolution of manufacturing processes has helped professionals use effective PCD equipment in various applications. For example, you can use the PCD tools for effective manufacturing from aluminum to composites and abrasive plates.
Better surface finish
High-quality surface finish is another benefit of PCD cutting tools; you don’t have to invest in a secondary operation. It implies that the product quality is maintained, but the money will be spent less than expected.
Select the right PCD cutting tools
There are many benefits to using the PCD cutting machine to meet your needs. If searching for the best tools to help the manufacturing process, check out the important considerations below.
Applications
These cutting tools are created under a rigorous process and developed with high quality in mind. The unique design construction improves various properties like tool lifespan, better throughput, and reduced ownership costs. If you are looking for a cost-effective way to manufacture high-quality products, select the PCD cutting tools without any doubt. A company requires PCD cutting tools for making precise and productive products. When choosing the PCD cutting machine, consider the type of material you will be cutting. As specified earlier, you need PCD for non-ferrous substances.
Specifications
PCD cutting tools are durable and can be used to process objects. For example, a polycrystalline diamond tool is ideal for processing various composites like fiber and metallic alloys. The cutting tools are available in three types such as piston series cutters, inserts, and hub cutters.
Wrapping up
Many manufacturing companies use various grades of PCD based on requirements like surface finish, life, depth of the cut, and material being cut. Find the right manufacturing tools to keep the process effective. Many companies offer cutting tools, but it is crucial to find a reliable name. The PCD cutting tools are a substantial investment but vital for manufacturing companies. Ensure that you get reliable tools from reputed sellers.